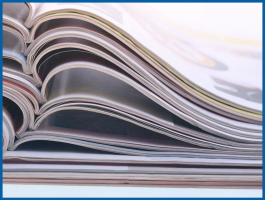
List of publications in 2022, in which our employees participated:
V. Barat, A. Marchenkov, V. Bardakov, D. Zhgut, M. Karpova, T. Balandin, S. Elizarov. Assessment of the Structural State of Dissimilar Welded Joints by the Acoustic Emission Method. Appl. Sci. 2022, 12(14), 7213. https://www.mdpi.com/2076-3417/12/14/7213 (full text). DOI: 10.3390/app12147213. https://www.ndt.net/article/appliedsciences/papers/applsci-12-07213.pdf (full text). eLibrary ID: 57774126
Abstract
In this study, we investigated defect detection in dissimilar welded joints by the acoustic emission (AE) method. The study objects were carbide and decarburized interlayers, which are formed at the fusion boundary between austenitic and pearlitic steels. Diffusion interlayers, as a structural defect, usually have microscopic dimensions and cannot be detected using conventional non-destructive testing (NDT) methods. In this regard, the AE method is a promising approach to diagnose metal objects with a complex structure and to detect microscopic defects. In this paper, the AE signatures obtained from testing defect-free specimens and specimens with diffusion interlayers are analyzed. We found that the AE signature for defective and defect-free welded joints has significant differences, which makes it possible to identify descriptors corresponding to the presence of diffusion interlayers in dissimilar welded joints.
V. Barat, A. Marchenkov, V. Bardakov, D. Zghut, M. Karpova, S. Elizarov. Diagnostics of Dissimilar Weld Joints of Austenitic to Pearlitic Steels by Acoustic Emission. J. Inst. Eng. India Ser. D. 2022. Pp. 531-538. DOI: 10.1007/s40033-022-00409-y. eLibrary ID: 59752924
Abstract
Dissimilar welded joints are widely used nowadays in power engineering industry for manufacturing of pipelines and other power equipment elements. Diagnostics of welding defects in these joints by nondestructive testing (NDT) is quite difficult, since high gradients of chemical composition and microstructure reduce the sensitivity of traditional NDT scanning methods. The paper is devoted to the study of the possibility of AE method application for diagnostics of dissimilar welded joints of pearlitic to austenitic steel. The identification of defects lack of penetration and microstructure defects in the form of diffusion interlayers under cyclic tensile loading of flat specimens with welded joints is considered. As a result of the research, it was found that dissimilar welded joints containing defects are characterized by a specific AE signature. It was established that for welded specimens with lack of penetration and diffusion interlayers, the AE activity turned out to be significantly higher than for defect-free ones. Herewith, specimens with diffusion interlayers are characterized by large amplitude values (up to 70–80 dB), and specimens with lack of penetration are characterized by higher AE activity, while the amplitudes of AE hits did not exceed 60–65 dB. The results obtained can be used for determination of diagnostic criteria for detecting defects by AE method and subsequent development of an industrial NDT technique for dissimilar welded joints under study.
V. Barat, A. Marchenkov, S. Ushanov, V. Bardakov, S. Elizarov. Investigation of Acoustic Emission of Cracks in Rails under Loading Close to Operational. Appl. Sci. 2022, 12(22), 11670. https://www.mdpi.com/2076-3417/12/22/11670 (full text). DOI: 10.3390/app122211670. eLibrary ID: 57722391
Abstract
The paper is devoted to the study of the possibility of detecting cracks in railway rails by the acoustic emission (AE) method. An experimental study of AE signals under cyclic compression loading of rail fragments, which simulates the rail operating load, has been carried out. Fragments of rails without defects, as well as fragments containing pre-grown fatigue cracks, were studied. It was found that AE signals generated by a rail with a crack have higher activity compared to signals from defect-free specimens. It is shown that the AE signals during the loading of defect-free specimens have a short duration and low amplitude and may be caused by the deformation of non-metallic inclusions. The crack presence leads to an increase in the AE hits rate and changes the nature of the distribution of the AE hits amplitudes. It is shown that the crack location has no effect on the reliability of its detection by the AE method. Criteria of crack detection by AE testing are offered as a result of this study.
A. Machikhin, A. Poroykov, V. Bardakov, A. Marchenkov, D. Zhgut, M. Sharikova, V. Barat, N. Meleshko, A. Kren. Combined Acoustic Emission and Digital Image Correlation for Early Detection and Measurement of Fatigue Cracks in Rails and Train Parts under Dynamic Loading. Sensors 2022, 22(23), 9256. https://www.mdpi.com/1424-8220/22/23/9256 (full text). DOI: 10.3390/s22239256. eLibrary ID: 57644948
Abstract
Fatigue crack in rails and cyclic-loaded train parts is a contributory factor in multiple railroad accidents. We address the problem of crack detection and measurement at early stages, when total failure has not yet occurred. We propose to combine acoustic emission (AE) testing for prediction of crack growth with digital image correlation (DIC) for its accurate quantitative characterization. In this study, we imitated fatigue crack appearance and growth in samples of railway rail and two train parts by cyclic loading, and applied these two techniques for inspection. Experimental results clearly indicate the efficiency of AE in the early detection of fatigue cracks, and excellent DIC capabilities in terms of geometrical measurements. Combination of these techniques reveals a promising basis for real-time and non-destructive monitoring of rails and train parts.
V. A. Barat, S. N. Lenev, Yu. A. Radin. Acoustic Method for Detecting Air Suction in the Vacuum System of Steam Turbine Plants of Thermal Electric Power Stations. Power Technology and Engineering. 2023. Vol. 56, No. 6. P. 910-917. DOI 10.1007/s10749-023-01609-6. eLibrary ID: 63230917
Abstract
Insufficient density of vacuum systems in steam turbines (STs) is one of the main causes of vacuum deterioration in their condensers. It considerably affects the power and efficiency of steam turbine plants (STPs) and deteriorates the coolant quality, which affects the reliability of pipe systems of regenerative heaters. Even at air flow rates exceeding 50 – 60 kg/h, the steam jet ejector, which exhausts air from a condenser, is overloaded and cannot maintain the absolute pressure in the condenser within permissible values. The presence of several zones of increased suction makes it preferable to use portable means of detecting the suction and determining its extent. Generally, this is achieved by employing methods based on application of inert gases, infrared thermography, and acoustic approaches. Experimental study involving the detection of suction at various ST zones operating under rarefaction in eight turbine units with types PT-70-130/13, PT-65/75-130/13, T-110/120-130, and T-290/335-240 of Mosénergo branches was performed using acoustic emission equipment and inert gases. The measurements were performed in locations exhibiting the highest probability of detecting suction, such as the areas of hatches and atmospheric safety valves of low-pressure cylinders, membranes and seals of the shaft of the STP, thermocouple channels, and flange coupling of shut-off valves. Using such an acoustic device enabled the development of suction maps for vacuum systems of STPs with various capacities in a bid to develop technical solutions based on them for eliminating suction and to develop algorithms for diagnosing the state of the vacuum system of STs
Yu. G. Matvienko, N. A. Makhutov, I. E. Vasil’ev, D. V. Chernov, V. I. Ivanov and S. V. Elizarov. Evaluation of the Residual Strength of Composite Products Based on the Structural-Phenomenological Concept of Damage and Acoustic Emission Diagnostics. Inorg Mater 59, 1504–1514 (2023). DOI: 10.1134/S0020168523150098. eLibrary ID: 65572356
Abstract
A structural-phenomenological concept of monitoring the residual strength of composite materials is proposed. The structural-phenomenological concept was developed taking into account the kinetics of damage and destruction of polymer composite material (PCM) at the micro-, meso-, and macroscale levels, which generate acoustic emission pulses (AE) recorded by the receiving transducers of the antenna array. A correspondence between the ongoing destruction of the composite material structure at the micro-, meso-, and macroscale level and the AE pulses recorded at the same time and their weight content provides the possibility of monitoring of the damage kinetics in the loading mode at all structural levels and, consequently, the possibility of control of the residual strength of the product. An algorithm and software have been developed that made it possible to divide the recorded AE signals into clusters of lower, middle, and upper energy levels corresponding to micro-, meso-, and macroscale disruptions of the structure of a composite material and calculate the AE activity and the weight content of location pulses in energy clusters, thus displaying the dynamics of their changes every second. Comparison of the current values of the most informative parameters of the weight content of location pulses in energy clusters with the threshold values recorded during the destruction of the material provides monitoring of the residual strength of the product in the loading mode. The validity of the developed concept, algorithm and software was proved during tests of elementary and structurally similar samples of PCM under different loading conditions. An example of using the developed technique for revealing the areas of the most intense damage accumulation in a MS-21 fuselage panel at a stepwise increase in the compressive load is presented. In addition to the possibility of identification of the area of intense accumulation of damage and failure of the structure of the composite material, the structural-phenomenological concept of the AE diagnostics provides also the possibility of tracing the damage kinetics at different scale-structural levels, controlling the level of the residual strength of the panel upon the stepwise compression
Sagaidak A.I., Bardakov V.V. Method for determining strength of concrete by acoustic emission method. Russian patent №2807868 (2022). eLibrary ID: 56017020
Abstract
Field: construction; concrete mixtures. Substance: scope of the invention relates namely to the control of concrete mixtures of various compositions using the method of acoustic emission signals during the formation of their structure. A method for determining the strength of concrete with chemical and mineral additives using the acoustic emission method is disclosed, which includes determining the parameters of acoustic emission signals and recording the time of their appearance in real time. To implement the method, a deep waveguide with an attached acoustic emission transducer is placed in the concrete mixture. On concrete cubes of different compositions measuring at least 200×200×200 mm the structure formation is monitored, and each composition is duplicated two to three times, and for each composition monitoring is carried out continuously for at least twenty-eight days. Next, the strength characteristics of the concrete are monitored, and the strength of the control cubes is monitored on the 1st, 3rd, 7th, 14th and 28th days of curing. After this, the relationships and dependencies of the informative parameters of the acoustic emission signals between the strength characteristics of concrete are established. Then, the informative parameters of acoustic emission signals, which closely correlate with the strength of concrete, are considered, and the optimal time intervals for measuring acoustic emission are established, which makes it possible to most accurately predict the kinetics of further strength gain of concrete using the acoustic emission method. After this, acoustic emission pulses are recorded in real time, and three stages of structure formation are distinguished, characterized by varying degrees of acoustic emission intensity. The start and end times of the second period are specified in an automated mode, in which the Akaike information criterion is used where AIC is the value of the Akaike criterion coefficient; – dependence of the number of acoustic emission pulses on time; N – duration of the observation interval; k – reference number. In this case, the change in the sign of the derivative of the Akaike function, which corresponds to the disorder of the process, is used as a detection criterion, and the moment when the criterion reaches a minimum is selected as the time. Within the framework of this algorithm, the Akaike criterion is applied twice - to determine the beginning and end of the second stage. Next, set the start and end times of each of the three stages, the parameters and are determined. The parameter is determined as the difference between the obtained values of the beginning and end of the second period, and the slope of the third perioddepending on the sum of acoustic emission pulses versus time. The parameter is determined by the least squares method in a time window, the beginning of which coincides with the beginning of the third stage, and based on the estimated parameters and . Then the strength of concrete is predicted in accordance with predictive models. SP-180 according to TU 20.59.59-003-26025492-2018 or CENTRIPOR TFM 411R are used as chemical additives, and ground and granulated blast furnace slag is used as a mineral additive. Effect: ability to determine the strength of concrete with chemical and mineral additives using the acoustic emission method, and the relative error of using an automated algorithm when predicting strength does not exceed 4.0%.
Y. A. Eliovich, V. A. Barat, V. V. Bardakov, A. Y. Marchenkov, D. D. Khokhlov and D. A. Zhgut. Predictive Analysis of Structural Changes in Paratellurite Crystals Using the Acoustic Emission Method. International Conference on Information, Control, and Communication Technologies (ICCT), 2022, pp. 1-5. DOI: 10.1109/ICCT56057.2022.9976555