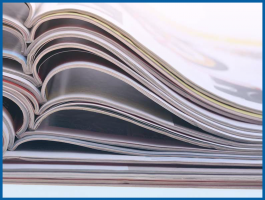
List of publications in 2016, in which our clients describe examples of the use of our company's products:
Skalsky V.R., Pochapsky Y.P., Klym B.P., Simakovych O.H., Tolopko Y.D., Velyky P.P., Dolishniy P.M. (Karpenko Physical and Mechanical Institute, NAS of Ukraine). Diagnostic system of wireless acoustic emission signal transfer for monitoring the oil-and-gas facilities. Science and Innovation. 2016. Vol. 12. No 1. P. 13-21. DOI 10.15407/scine12.01.013. eLibrary ID: 45321507
A. E. Burov, A. M. Lepikhin. Numerical simulation of carrying capacity of the high-pressure metal composite vessel. Journal of Machinery Manufacture and Reliability. 2016. Vol. 45. No 5. P. 443-450. DOI 10.3103/S1052618816050071. eLibrary ID: 27579867
Abstract
This paper considers the issue of the numerical simulation of stress–strain state and the destruction of the composite vessel with a metal liner under gradually increasing pressure. The provided solution algorithm is based on the continuum of damage mechanics simulation that relates to the initiation of damage and the accumulation and degradation of the mechanical properties of material. The calculation results are compared with the actual experiment data.
Novikov E.A., Oshkin R.O. Method for determining the number of unfrozen water content in frozen soil. Russian patent № 2580316 (2016). eLibrary ID: 37389895
Abstract
Field: drilling of soil or rock. Substance: invention can be used in the design of buildings and structures to determine the amount of unfrozen water in frozen soils. To do this, carry out drilling with coring, thawed frozen soil sample is obtained and determine the total water content of continuous change in the course of an informative indicator of thawing. As an informative indicator of the ratio of use of acoustic emission activity of the monitored area to the array of acoustic emission activity of the most water-saturated area of the core is completely thawed; both figures take into account the specific weight of the soil and averages, consistent and comparable for the duration of the time intervals to determine the distribution of the total moisture content in depth. Registration of acoustic emission is carried out by converters to be placed on the depth of the hole array. Amount of unfrozen water in different parts of the array is calculated from the product of said index and informative total moisture content of the cores obtained at the same depth and in the same well as the corresponding value of the indicator. Effect: invention provides a method of control of the geological environment.
Gorbachev O.V., Samokhvalov S.Ya., Artyukhov D.I. Fibre optic acoustic-emission method for determining plastic deformations of large engineering structures. Russian patent №2650799 (2018). eLibrary ID: 41030368 (full text)
Abstract
Field: physics. Substance: signal of acoustic emission (AE) is generated by a brittle hardening glue, and is recorded using a multimode fibre optic distributed sensor. The glue is applied to an optical fibre, which serves as a distributed sensing element (DSE), when it is mounted on an engineering structure. After hardening, the glue becomes brittle and not only fixes optical fibre on the object, but also generates the AE signal when it is cracking, in case of plastic deformation of the controlled object (engineering structure). This method has a very high sensitivity, since the AE signal appears in the immediate vicinity of the sensor (DSE). Therefore, an acoustic-emission wave, which is practically not weakened, is almost completely transformed into an optical wave, and then into an electrical signal. The distributed sensor (DSE) glued to the engineering structure registers any plastic deformation, which leads to cracking of the brittle layer - hardened glue applied directly to fibre optics, for its entire length. Effect: increasing the sensitivity while reducing hardware costs, expanding the frequency spectrum of recorded signals, the ability to detect areas at an early stage, on which the destruction of the controlled object can occur, the ability to continuous remote monitoring
Yu. G. Matvienko, , I. E. Vasil’ev, A. V. Pankov, M. A. Trusevich (Blagonravov Mechanical Engineering Research Institute, Russian Academy of Sciences, Moscow; Zhukovskii Central Aerohydrodynamics Institute, Zhukovskii). Early Diagnostics of Damage and Fracture Zones in Composite Materials Using Brittle Strain Gauges and Acoustic Emission. Inorg Mater 53, 1484–1495 (2017). DOI: 10.1134/S0020168517150109
Abstract
The integrated use of the acoustic emission technique and brittle oxide strain gauges for testing the deformation of damage and fracture zones in samples of polymer composite materials (PCM) at the early phases is considered. For the realization of the proposed technique, integrated parameters were used and software including the cluster analysis and the classification of registered AE pulses was developed, which made it possible to differentiate crack formation signals in the brittle layer of a strain gauge from all the other signals that occur at the early phase of the deformation of PCM samples in the online mode. The use of acoustic emission testing and control video recording for the registration of cracks in a brittle oxide strain gauge with the threshold deformation value of 1000 μm/m provided the precise diagnostics of the forthcoming fracture zone in a sample at the early loading phase under the load level of 10–15% of the limiting one long before the beginning of the active PCM structural degradation phase and made it possible to determine the distribution fields of the highest main deformations in the region of a strain gauge and to perform their quantitative evaluation
Novikov E.A., Oshkin R.O., Shkuratnik V.L., Epshtejn S.A. Method of determining thermal resistance of coals. Russian patent № 2593441 (2016). eLibrary ID: 37406896
Abstract
Field: metrology. Substance: invention relates to metrology, particularly to means of measuring heat resistance of coals. Method involves applying two successive thermal shocks on coal sample, wherein second shock has higher intensity than the first one, and recording parameters of acoustic emission. Orientation of sample relative to heating source is constant. Recording of parameters of acoustic emission is performed at heating stages, and at the stages of cooling the sample after each of the thermal shocks. Determining the boundaries of time intervals corresponding to regions of peak values of acoustic emission, when its level is not less than one and half times higher than the level of background noise. In each of these intervals average values of acoustic emission activity are calculated. Acoustic emission activity level during the second thermal shock action, which is rendered to sample not containing moisture, indicates the number of damaged structural links, and the same parameter, but during further cooling, indicates the number of the preserved structural links, changing of stressed state to initial state. Then in relation to values of average acoustic emission activity during heating and cooling the coefficient of thermal resistance geomaterial is calculated. Effect: technical result is improvement of reliability and accuracy of measurements.
I. A. Rastegaev, A. V. Danyuk, D. L. Merson, A. Yu. Vinogradov (Tolyatti State University, Tolyatti). Universal Educational and Research Facility for the Study of the Processes of Generation and Propagation of Acoustic Emission Waves. Inorg Mater 53, 1548–1554 (2017). DOI: 10.1134/S0020168517150158
Abstract
The design and the algorithm for the use of an approved universal educational and research facility is described. The facility is designed to simulate a wide range of model controlled objects (vessels, pipelines, tube furnaces, reservoirs, etc.) and the main acoustic emission (AE) sources: cracks, leaks, corrosion damage, sites damaged by an aggressive medium, etc. The AE simulators installed at the facility are equipped with waveguides to provide the acoustic connection and protect the main elements of the facility in case of fracture of the simulators. The AE simulators are controlled using a loading device to preset the fracture initiation point and the simulator fracture rate. The facility is designed so as to provide low-cost repeated simulation of diverse situations that occur during the operation and examination of dangerous industrial objects. The facility can be used for research, education, and certification of personnel, techniques, and AE hardware; thus, it is useful for nondestructive testing laboratories
G. A. Sobolev, A. V. Ponomarev, Y. Y. Maibuk (Schmidt Institute of Physics of the Earth, Russian Academy of Sciences). Initiation of unstable slips–microearthquakes by elastic impulses. Izvestiya, Physics of the Solid Earth. 2016. Vol. 52. No 5. P. 674-691. DOI 10.1134/S106935131605013X. eLibrary ID: 27576219
Abstract
A series of laboratory experiments have been carried out with a model of two granite blocks under biaxial compression loading. The experiments are mainly intended for assessing the possibilities of partially releasing the accumulated potential energy. The model was subjected to calibrated mechanical impacts (strokes) which induced elastic impulses. The mechanical stresses, strains, and acoustic emission were recorded. The strokes caused both large slips releasing the stresses down to their initial level and small slips which reduced the stresses by 5–8%. The small slips mostly occurred after the precursory emergence of the low frequency oscillations having low amplitudes. Before the large slips, the stages of speeding-up of the relative motion of the sides of the block contact was observed, similar to those emerging before the natural slips unrelated to the strokes. This feature was not universal: in some cases, the model recovered to the stationary state of the block contact without a large slip. All the slips occurred with a time delay after the stroke. The time delay was shorter when the energy of the blow was higher. With the shorter time delays, the small slip is more likely to occur. The energy of the impacts was by three orders of magnitude lower than the energy accumulated by the model, which points to the triggering mechanism of slip initiation. The series of strokes resulting in the small displacements partially reduced the accumulated energy and prevented the emergence of large motions such as the stick-slip events. If after a series of such blows a large sliding event still occurred, its energy was higher than in the slips unrelated to the impacts. The experiments revealed the difficulties in solving the problem of earthquake hazard reduction by elastic impacts.
S. S. Kholodov, M. V. Grigor’ev, N. A. Shchipakov, N. O. Yakovlev, A. N. Lutsenko (Scientific-Educational Center Welding and Control, Bauman Moscow State Technical University, Moscow; All-Russian Scientific Research Institute of Aviation Materials, Moscow). Acoustic emission monitoring of damaging of fiberglass. Polym. Sci. Ser. D 9, 411–414 (2016). https://link.springer.com/article/10.1134/S1995421216040079 DOI: 10.1134/S1995421216040079