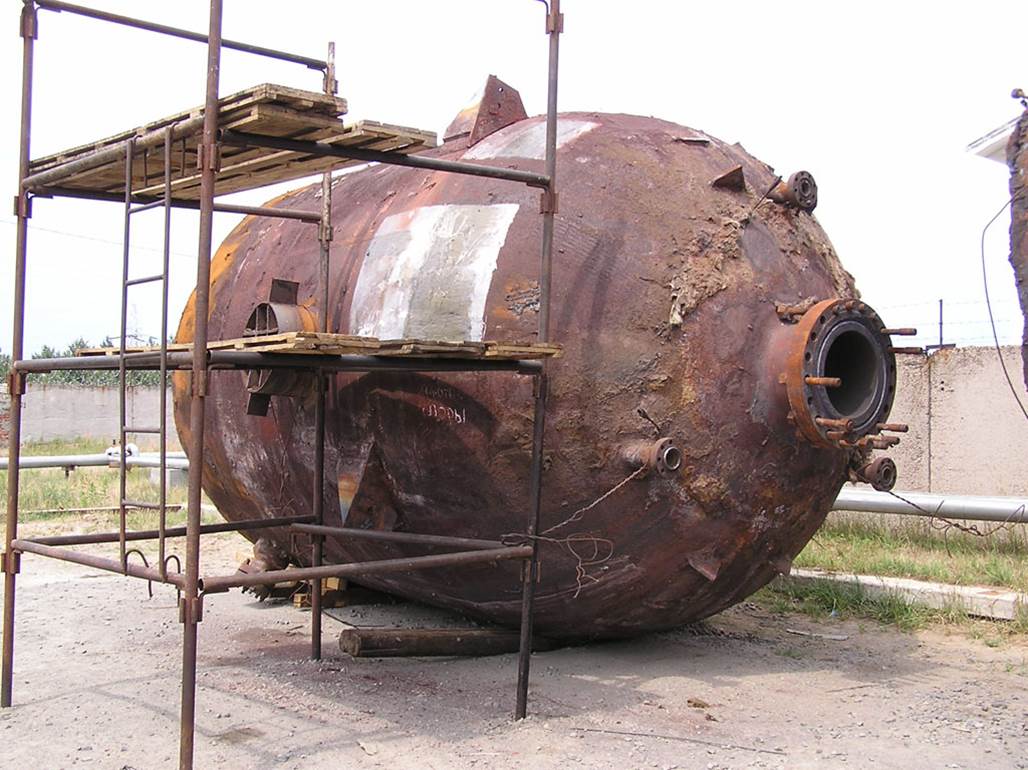
Structurally, the hydrotreater is a thick-walled vertical steel vessel. The inner surface of the hydrotreater is protected from the influence of an aggressive medium by a cladding layer. The high operating temperatures of the hydrotreater (from 320°C to 425°C), the aggressive environment and high operating pressure are factors that can lead to the generation and catastrophically rapid flaw growth, especially when the cladding layer is destroyed, which can induce hydrogen embrittlement and a decrease in the strength of the material.
The main diagnostic method of SHM-system was the method of AE testing. The AE handling part was represented by 18 AE sensors GT200UB (130-200 kHz), grouped into 6 belts, 4 on the hydrotreater shell and 1 belt on each lid. Sensors were mounted on waveguides to ensure the temperature allowed for the sensor is not exceeded. Temperature, vibration and pressure sensors were also installed.
By May 2007, the state of the hydrotreater had deteriorated. It was found to have 9 active zones, corresponding to AE sources with varying degrees of danger. The activity of some zones increased significantly, which indicated a progressive flaw growth and the possibility of the hydrotreater destruction. The source found in zone #5 and characterized by 370 events, was considered to be critically active.The results of the cluster analysis confirmed a previously determined assessment of the degree of danger of the AE source located in zone No. A final decision was made to stop the reactor.
At the dismantled reactor, work was carried out on the NDT in order to establish the reasons for the transition of the reactor to the limiting state. Based on the results of the internal examination, numerous violations of the integrity of the clad layer (up to its complete absence in some areas) were found. Dimensions of damage reached 5 mm. Based on the results of ultrasonic testing, numerous discontinuities in welded seams and separation of the base metal were revealed. The length of discontinuities along the length is 100 mm, in depth 15 mm. In one of the most active zones, discontinuities were detected both in welded seams and in the weld zone. Certain discontinuities occur at different depths, from 26 to 80 mm. These damages indicate significant degradation with loss of mechanical properties of the metal, which leads to brittle fracture of the object. Thus, the use of SHM-system allowed, on the one hand, to extend the lifetime of the reactor by 6 months, and on the other hand, to prevent the destruction of the reactor during operation with all the ensuing consequences.