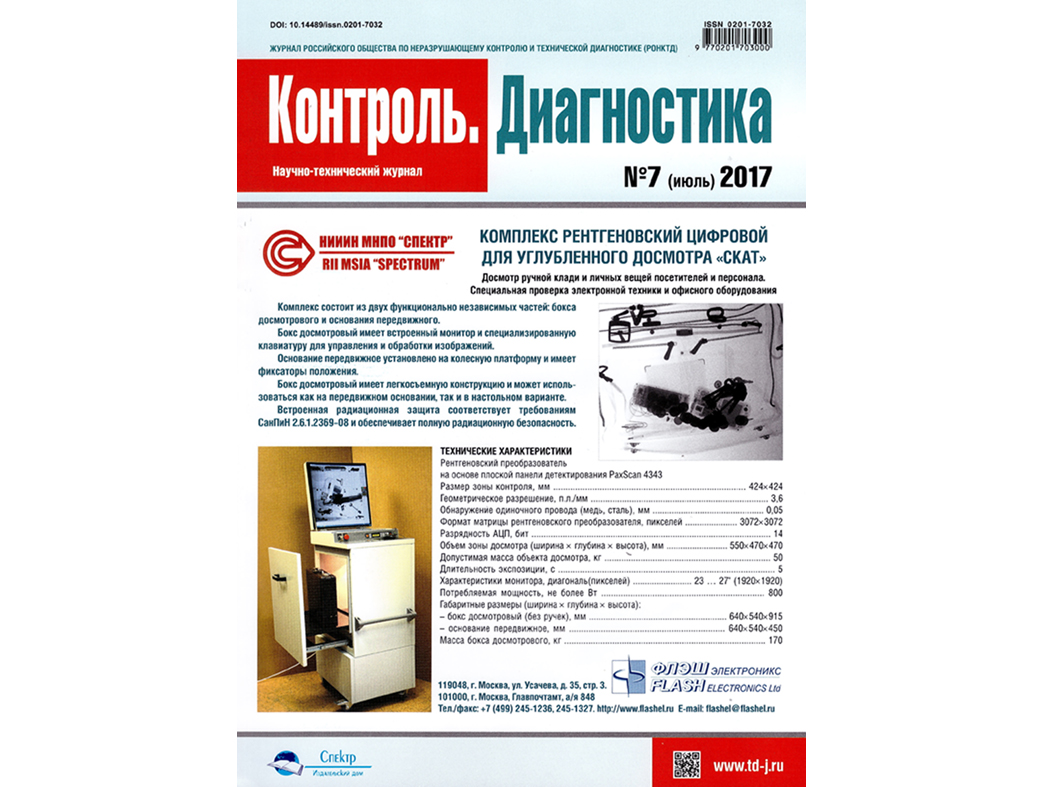
АЭ контроль динамического оборудования на примере роликовых опор вращающихся печей.
На глиноземном комбинате в цехах спекания и кальцинации методом акустической эмиссии обследовано 15 опорных блоков с различными сроками эксплуатации. Целью диагностики являлась разработка методики АЭ контроля, позволяющей контролировать оборудование без дополнительного нагружения и вывода вывода из эксплуатации. Исследованы возможности проведения непосредственно в рабочем режиме фильтрации акустических шумов, локации повреждений и идентификации типа повреждения.
На основании информации об известных дефектах по АЭ данным были идентифицированы такие дефекты, как усталостные трещины на галтельных переходах, износ поверхности вала при фрикционном контакте, трещины внутреннего кольца подшипника и бринеллирование, а также нарушение режима смазки.
Ключевые слова: акустическая эмиссия, режим эксплуатации, роликовые опоры, вал, подшипник
1. Введение
Традиционно акустико-эмиссионный (АЭ) контроль проводится для объектов, выведенных из эксплуатации. Такое требование связано как с действием эффекта Кайзера, приводящим к необходимости превышения тестовой нагрузки над рабочей, так и с повышенным уровнем акустических и электромагнитных шумов в режиме эксплуатации объекта.
Однако проведение АЭ контроля в режиме эксплуатации допустимо при условии увеличения периода сбора АЭ данных и разработки специализированной методики, которая должна учитывать влияние различных технологических и внешних акустических шумов, особенности нагружения объекта в рабочем режиме, действие повреждающих факторов и возможные механизмы разрушения объекта.
Рис. 1. Вращающаяся печь, опирающаяся на парные роликовые опоры.
Обозначены: 1 – печь, 2 – опорные ролики, 3 –фундамент опоры
В данной работе исследована возможность проведения АЭ контроля роликовых опор вращающихся печей без вывода их из эксплуатации. Экспериментальные работы проводились на территории глиноземного комбината в цехах спекания и кальцинации, а также в ремонтном цеху.
Объектом контроля являлась роликовая опора вращающейся печи (рис. 1). Печь представляет собой цилиндр диаметром до 5 и длиной до 185 м, установленный с наклоном. Она предназначена для спекания руды с целью образования твердых алюминатов. Печь опирается на 7-8 парных роликовых опор. Наиболее нагружены опоры, установленные в разгрузочном конце.
Рис. 2. Схема роликовой опоры
Каждая парная роликовая опора состоит из 2 опорных блоков – правого и левого, установленных на общий фундамент. Каждый блок состоит из вала, запрессованного на него опорного ролика и 3 подшипниковых узлов, смонтированных в 2 корпусах (рис. 2). Период оборота печи равен 50 с, период оборота ролика опоры – 12.5 с. Срок эксплуатации контролируемых опор составлял от 1 года до 13 лет.
Роликовая опора является сложным и ответственным элементом конструкции печи. При ее поломке проводится экстренная остановка оборудования, а также замена неисправных элементов. Такая остановка приводит к простою печи, а значит к большим денежным затратам. Из 200 опорных блоков на комбинате в среднем за год 5 блоков выходит из строя из-за поломки подшипников и еще 1 блок – из-за разрушения вала. Поэтому при проведении АЭ диагностики необходимо обеспечить выявление дефектов всех ее элементов – и вала, и ролика, и подшипников.
Ролик – это часть опорного блока, которая непосредственно соприкасается с печью, основные дефекты на нем – задиры и выкрашивание металла.
Вал является цельнометаллическим литым элементом конструкции. При вращении печи происходит циклическое нагружение вала в радиальном и осевом направлении. Повреждения вала могут возникать на всех стадиях его эксплуатации. Вначале проявляются дефекты, допущенные при изготовлении вала – поры, раковины, термические трещины. При продолжительной эксплуатации возникают усталостные трещины, а также происходит усталостный и абразивный износ вала. Поскольку роликовые опоры эксплуатируется при неблагоприятных температурных условиях, при высоком уровне вибрации и в условиях циклического нагружения, наиболее вероятным дефектом вала является образование усталостных трещин.
К основным элементам подшипника относятся наружное кольцо, внутреннее кольцо, цилиндрические тела качения и сепаратор. Разрушение подшипника происходит по 3 основным причинам. Первая – неправильный монтаж подшипника, при котором могут возникать концентраторы напряжений, связанные как с повреждением сепаратора, так и с несоосностью вала и подшипника или разбалансировкой подшипника. Вторая причина – недостаточное количество или низкое качество смазочных материалов. При попадании пыли и грязи в смазочный материал образуется абразивный слой, который истирает металл и ведет к образованию концентраторов напряжений. При высыхании или отсутствии смазочных материалов возникают натиры, которые также ведут к образованию концентраторов напряжений и разрушению объекта. Третья причина – усталостное разрушение подшипника. Как известно, исследуемый объект испытывает циклическое нагружение. С течением времени уровень накопленных повреждений достигает критической отметки, что приводит к пластической деформации и трещинообразованию в элементах подшипника. К дефектам подшипника, основанным на пластической деформации, можно отнести усталостное выкрашивание и бринеллирование.
Поскольку вал является монолитной цельнометаллической конструкцией с многочисленными выступами и перепадами толщины, проведение НК вала традиционными сканирующими методами оказывается затруднительным даже для роликовых опор, выведенных из эксплуатации.
Из-за низкой угловой скорости (1 оборот за 12.5 с) для контроля подшипников роликовых опор не вполне подходит хорошо известный метод виброметрии.
В то же время, ряд лабораторных исследований с заранее заготовленными дефектами [1-4] и случаи успешного проведения АЭ мониторинга роликовых опор вращающихся печей [5] показывают, что метод АЭ, применительно к контролю целостности роликовых опор, может быть использован в режиме эксплуатации. Он обладает высокой чувствительностью, позволяя обнаруживать дефекты вне зависимости от их вида и формы, а также скорости вращения опоры [5].
Обобщая все вышесказанное, можно сделать вывод о том, что контроль роликовых опор вращающихся печей без их вывода из эксплуатации – задача, которая может с высокой достоверностью быть решена при помощи метода АЭ.
2. Предварительные исследования
Применялись преобразователи акустической эмиссии (ПАЭ) типа GT200 (компания «ГлобалТест», г. Саров) с рабочим частотным диапазоном 130-200 кГц. Сигнал с преобразователей предварительно поступал на предусилитель производства компании «ИНТЕРЮНИС-ИТ» (Москва), с коэффициентом усиления 26 дБ и частотным фильтром 30–500 кГц. В качестве системы сбора данных использовался 4-канальный внешний USB-модуль ввода-вывода «E20-10» производства компании «L-Card» (Москва) и универсальный прибор неразрушающего контроля «UNISCOPE» компании «ИНТЕРЮНИС-ИТ». Выходные данные модуля «E20-10» представляли собой имеющую произвольную длительность непрерывную временную реализацию АЭ сигнала с частотой дискретизации 2.5 МГц. «UNISCOPE» использовался в режиме АЭ системы, записывая стандартные акустикоэмиссионные параметры и осциллограммы принятых сигналов длительностью до 1000 мкс [6].
2.1. Исследование шумов
При НК роликовых опор вращающейся печи в режиме ее эксплуатации достаточно высок уровень шума в звуковом диапазоне. Его источниками являются процессы, происходящие внутри печи (движение шихты), также присутствуют шумы приводного двигателя, шумы незакрепленных деталей при вращении печи и шумы, возникающие при вращении сборного бандажа. Однако, в диапазоне выше 30 кГц благодаря точечному сухом контакту между бандажом печи и роликом акустические шумы, как правило, составляют не более 32 дБ в самой неблагоприятной точке конструкции – в месте подачи шихты. Единственным значимым внешним источником акустических шумов являются задиры и шероховатости на поверхности ролика или бандажа печи. При соприкосновении с местом задира возникает сигнал АЭ с амплитудой до 100 дБ. Однако, такие мешающие сигналы легко могут быть исключены из дальнейшего анализа, поскольку их регистрация происходит с определенным периодом, равным периоду вращения роликовой опоры, либо печи (рис. 3).
Рис. 3. АЭ сигналы с периодом 12.5 с и 50 с, связанные с задирами и шероховатостями на поверхности ролика или бандажа печи
Также обнаружено, что электромагнитные наводки не превышают 40 дБ и, таким образом, не оказывают существенного влияния на результаты АЭ контроля.
2.2. Калибровочные измерения
В ремонтном цеху были проведены измерения затухания и скорости распространения акустического сигнала на выведенном из эксплуатации опорном блоке со снятыми торцевыми крышками. Для имитации источников АЭ был использован электронный имитатор, излучения производились на валу в области галтельного перехода и на торцах, а также на внутренних и на внешних кольцах подшипников (рис. 4).
Рис. 4. Схема роликовой опоры со снятыми защитными крышками. Точки, в которых проводились излучения имитатором, и рекомендуемые места установки ПАЭ
В пределах вала коэффициент затухания составил 5 дБ/м, скорость распространения акустических волн – 3776 м/с. Выявлено наличие высокого значения затухания (30-35 дБ) на границе «корпус подшипника – вал». Поэтому при излучении имитатором на одном из подшипников, амплитуда принятых сигналов на подшипнике, находящемся вблизи противоположного торца, не превышала уровень шумов.
Из полученных результатов следует, что АЭ контроль необходимо производить следующим образом (рис. 4). Для полноценного контроля всех 3 подшипников, включающего зонную локацию с точностью до элемента конкретного подшипника, требуется установить ПАЭ во всех имеющихся точках доступа, а именно по 3 ПАЭ на каждом из 2 подшипниковых корпусов (рис. 5). Поскольку длина вала невелика (4050 мм), для его полноценного АЭ контроля, включающего проведение линейной локации, достаточно обеспечить доступ к валу, сняв крышки, и установить на торцах 2 ПАЭ: 1 со стороны упорного подшипника и 1 с противоположной стороны (рис. 6). Медленное вращение ПАЭ на торцах вала не вызывает значительных технических сложностей при длительности проведения АЭ контроля порядка 1 ч.
Рис. 5. ПАЭ, установленные на корпусе подшипников |
Рис. 6. ПАЭ, установленный на торце роликовой опоры со снятой защитной крышкой |
3. АЭ контроль
Следующий этап работы – проведение АЭ контроля опоры без вывода объекта из эксплуатации. АЭ данные снимались при штатном вращении печи и опоры в течение 1-2 ч. Было исследовано 5 опорных блоков с открытыми крышками, где был обеспечен непосредственный доступ и к подшипникам, и к валу. Также было обследовано 10 опорных блоков с закрытыми крышками, где доступ для контроля имелся только к подшипникам.
3.1. АЭ контроль подшипников
В одном из подшипников высохла смазка, что привело к интенсивному трению и возникновению скрежета в звуковом диапазоне. ПАЭ также зафиксировали сигналы с амплитудой около 100 дБ и длительностью более 100 000 мкс (рис. 7). Таким образом, путем идентификации такого рода сигналов можно проводить оценку состояния смазочного материала.
Рис. 7. АЭ сигнал, зарегистрированный на корпусе подшипника. Пересыхание смазки
АЭ диагностика позволяет выявлять не только дефекты подшипника, но и предразрушающие состояния, характеризующиеся образованием и накоплением повреждений в различных частях конструкции подшипника. Источником АЭ сигналов на этой стадии может быть пластическое деформирование или малое абразивное истирание поверхности, возникающее при попадании пыли или грязи в смазочный материал. Такие процессы характеризуются потоком низкоамплитудных АЭ сигналов.
На роликовой опоре, введенной в эксплуатацию 1 год назад, зарегистрированы сигналы с амплитудой до 60 дБ, длительностью порядка 100 мкс и активностью около 3‑4 с-1 (рис. 8). На основании сходства с импульсами от вдавливания индентора [7], они были отнесены к бринеллированию подшипника.
Рис. 8. АЭ сигнал, зарегистрированный на корпусе подшипника. Предположительно бринеллирование.
На роликовой опоре, введенной в эксплуатацию 3 года назад, наблюдались более высокая активность (до 10‑12 с-1) и более высокие амплитуды (до 76дБ) АЭ сигналов (рис. 9), что свидетельствует о том, что процесс накопления повреждений переходит в более интенсивную фазу – накопления повреждений.
Рис. 9. АЭ сигнал, зарегистрированный на корпусе подшипника. Стадия накопления повреждений
Заключительной стадией процесса накопления повреждений является образование дефектов, например усталостное выкрашивание или появление трещин. При этом происходит существенное изменение характера потока АЭ сигналов – растет активность, появляются амплитудные тренды, и, главное – обязательно имеется периодичность появления, вызванная тем, что акустические сигналы на данной стадии возникают при периодическом соударении ролика подшипника с местом повреждения.
На подшипнике одной из опор обнаружен умеренно активный источник АЭ (рис. 10), который, вследствие невысокого характерного уровня амплитуд, не проходил процедуру подтверждения.
Рис. 10. Периодический АЭ сигнал, зарегистрированный на корпусе подшипника. Умеренно активный источник АЭ
Более мощный периодический источник АЭ (около 100 дБ), обнаруженный на другой опоре (рис. 11), оказался трещиной внешнего кольца подшипника.
Рис. 11. Периодический АЭ сигнал, зарегистрированный на корпусе подшипника. Трещина внешнего кольца
Таким образом, на основе параметров потока АЭ сигналов возможна идентификация как катастрофических источников, так и умеренно активных. Проведение регулярной АЭ диагностики роликовой опоры с потенциально возможным дефектом подшипника позволяет оценивать и прогнозировать интенсивность накопления повреждений.
3.2. АЭ контроль вала
АЭ сигнал, характерный для процесса трения – это непрерывный случайный процесс, характеризующийся распределением амплитуд импульсов, близким к нормальному, что не характерно для трещин. Обнаружено, что более высокие среднеквадратичные значения (СКЗ) амплитуды акустического сигнала наблюдаются у роликовых опор с большим сроком эксплуатации, что позволяет сделать вывод о том, что СКЗ амплитуды АЭ сигнала характеризует интегральную степень износа поверхности вала. На рис. 12 приведены сигналы, полученные при диагностике валов роликовых опор, находящихся в эксплуатации 2 и 9 лет.
Рис. 12. АЭ сигналы, полученные при диагностике валов роликовых опор, находящихся в эксплуатации 2 и 9 лет
Появление на фоне непрерывного сигнала отдельных импульсов большой амплитуды (до 81 дБ) может свидетельствовать о начале разрушения поверхности вала опорного блока при фрикционном контакте (рис. 13).
Рис. 13. АЭ сигналы, полученные при диагностике валов. Начало разрушения поверхности вала при фрикционном контакте
Рис. 14. Осциллограммы АЭ сигналов, зарегистрированных на валах 2 роликовых опор, и результаты линейной локации
Соответствующая образованию и росту трещин АЭ имеет принципиально дискретный и апериодичный характер. При подрастании трещины генерируются, как правило, высокоамплитудные импульсы, с определенным характерным распределением параметров потока данных АЭ. При контроле опорных блоков на 2 валах, находящихся в эксплуатации 11 и 13 лет, зарегистрированы источники АЭ с амплитудами до 78 дБ и активностью около 10‑20 с-1 (рис. 14), которые, судя по осциллограммам и распределению АЭ параметров, предположительно, соответствуют активным усталостным трещинам. Анализ линейной локации показал, что источники АЭ располагаются в области галтельных переходов, т.е. в местах с наибольшей концентрацией напряжений. В соответствии с ПБ 03-593-03 [8], выявленные источники оказались относящимися к I и II классам опасности и по этой причине не проходили процедуру подтверждения.
Выводы
1. Исследована возможность проведения АЭ контроля роликовых опор вращающихся печей без вывода их из эксплуатации.
2. В диапазоне частот выше 50 кГц внешние шумы составляют не более 32 дБ. Исключением являются сигналы, связанные с задирами и шероховатостями на поверхности ролика или бандажа печи, которые регистрируются с периодом, равным периоду вращения роликовой опоры, либо периоду вращения печи.
3. Для полноценного контроля всех 3 подшипников, включающего зонную локацию с точностью до элемента конкретного подшипника, необходимо установить по 3 ПАЭ на каждом из 2 подшипниковых корпусов. Для полноценного АЭ контроля вала, включающего проведение линейной локации, достаточно обеспечить доступ к валу, сняв крышки, и установить 2 ПАЭ на его торцах.
4. АЭ сигналы с амплитудой около 100 дБ и длительностью более 100 000 мкс свидетельствуют о проблемах со смазочным материалом.
5.Появление в потоке АЭ данных периодической закономерности и амплитудных трендов может быть критерием оценки образования повреждений подшипников, соответствующих предельному состоянию конструкции.
6. СКЗ амплитуды непрерывного АЭ сигнала характеризует интегральную степень износа поверхности вала.
7. При контроле 2 опорных блоков в области галтельных переходов обнаружены трещиноподобные источники I и II класса опасности.
Список литературы
1. Abdullan M. Al-Ghamd, D. Mba // A comparative experimental study on the use Acoustic Emission and vibration analysis for bearing defect identification and estimation of defect size / Mechanical Systems and Signal Processing.#4(8).2006. pp. 1537-1571.
2. Yongyong He, Xinming Zhang, Michael L. Friswell // Defect Diagnosis for Rolling Element Bearing Using Acoustic Emission / Journal of Vibration and Acoustics. #131(6). 2009.
3. Kristoffer Bruzelius, D. Mba // An initial investigation on the potential applicability of Acoustic Emission to rail track fault detection. #37(7). 2004. pp. 507-516.
4. Dorra Baccar, Sandra Schiffer, Dirk Söffker // Acoustic Emission-based identification and classification of frictional wear of metallic surfaces / 7th European Workshop on Structural Health Monitoring. 2014. pp. 1178-1185.
5. Miettinen, J., Pataniitty, P. // Acoustic Emission in Monitoring Extremely Slowly Rotating Rolling Bearing / Proceedings of COMADEM ´99. 1999. Pp. 289-297.
6. Елизаров С.В., Алякритский А.Л., Барат В.А., Трофимов П.Н., Кольцов В.Г., Шиманский А.Г., Щелаков Д.А. Новый портативный инструмент НК "UNISCOPE". Территория NDT, № 2, 2012. Стр. 65-68.
7. V.M. Matyunin, V.A. Barat, V.V. Bardakov, A.Yu. Marchenkov // Assessment of Fracture Toughness of Hardening Coatings by Instrumented Indentation and Acoustic Emission Parameters / Proceedings of 3rd International Scientific Symposium “Sense. Enable. SPITSE.” 2016. National Research University "MPEI", Moscow ― Smolensk, Russia, 20 June – 01 July 2016. Pp. 95-96.
8. ПБ 03-593-03. Правила организации и проведения акустико-эмиссионного контроля сосудов, аппаратов, котлов и технологических трубопроводов (утверждены постановлением Госгортехнадзора РФ от 9 июня 2003 г. №77).
9. Патент РФ №2411150. Способ диагностики подшипников качения букс подвижного состава железнодорожного транспорта и метрополитена. 2011 г.